Home Cuppa Convos Technical Snapshots Technical Snapshot: Why Do Liquid Membranes Crack?
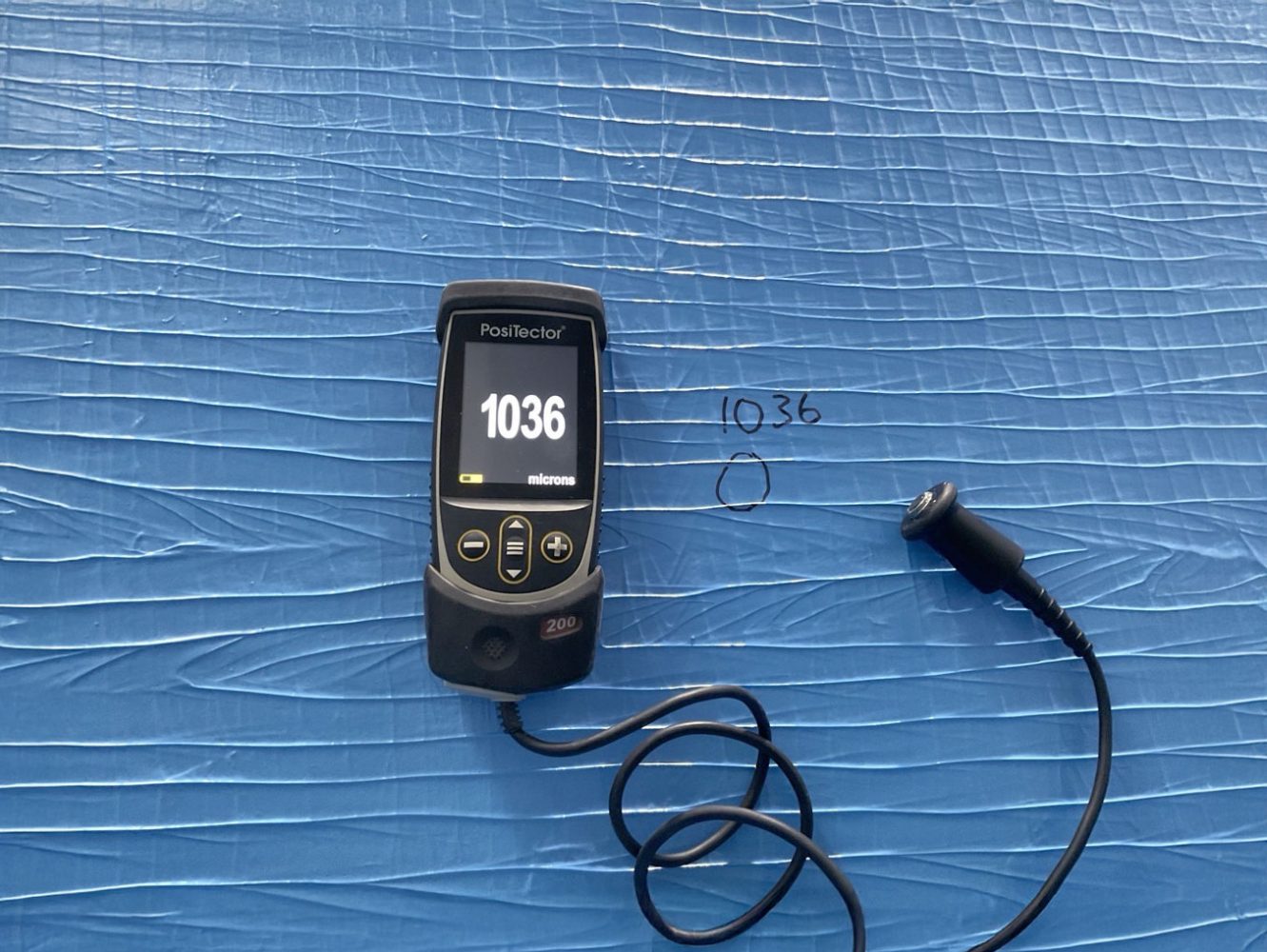
Technical Snapshot
Issue: Why Do Liquid Membranes Crack?
You’ve applied a liquid waterproofing membrane system, only to discover cracks forming after it has cured. Not what you were expecting, right?
Cracks in a waterproofing membrane can compromise the entire system, allowing water to penetrate and cause damage to the substrate. But why do these cracks appear?
Key reasons could include:
Substrate Movement: Over time, buildings naturally settle, and substrates shift due to temperature changes and structural movement. If the liquid membrane lacks sufficient membrane elongation to handle these shifts, cracks can occur, especially around corners and joints.
Applying a flexible bandage at these high-stress points adds reinforcement and allows the membrane to flex with the substrate, reducing the risk of cracking. Using a flexible membrane designed for dynamic movement can help prevent these cracks.
Improper Curing Times: Rushing the curing process can weaken the bond between the liquid membrane and the substrate, increasing the likelihood of cracks. Allowing sufficient curing time is essential to ensure the membrane’s strength and flexibility, particularly in wet or high-traffic areas. Remember, patience during curing prevents future cracks!
Improper Application Thickness: Applying the membrane too thin can lead to insufficient coverage, while too thick can cause curing issues. Both scenarios increase the risk of cracking. Following the manufacturer’s guidelines for even application ensures the membrane performs properly.
Incorrect
Pic 1. Flexi Bandage under membrane could’ve prevented cracks
Pic 2. Insufficient epoxy primer curing times is a membrane killer
Pic 3. Improper application thickness will put your membrane at risk
Solution
Using the below techniques can help to avoid membrane cracking:
Use Flexible Membranes: Opt for a liquid membrane that conforms to the substrate’s movement. According to AS 4654.2, ‘Waterproofing membranes should be capable of accommodating structural movement and offer proper membrane elongation.’
Choose products designed with flexibility to handle the building’s natural shifts.
Don’t Rush Curing: Allow the membrane the full recommended time to cure to maximise its adhesion and flexibility, helping it withstand substrate movement and environmental stresses effectively.
Apply the Correct Thickness: Refer to the manufacturer’s instructions on membrane thickness. As outlined in AS 4654.2, ‘Membranes should be applied at a uniform thickness to prevent premature failure.’
Using tools like a notched trowel or roller ensures consistency.
Consider Reinforcement Fabric: Reinforcing fabric is an excellent method to bolster the membrane in areas that are prone to movement. This extra step can prevent cracking in high-stress spots.
By following these best practices and adhering to the relevant Australian Standards, you’ll ensure your liquid membrane remains intact and fully functional, providing long-term waterproofing protection.
Do you have a technical issue you need help with? Reach out to Bayset’s Technical Team to get a solution that best suits your needs: 1300 BAYSET
Correct
Pic 4. Use tools like a PosiTector to achieve the required thickness
Pic 5. A Wet Film Thickness gauge helps to create even application
Pic 6. A coat of primer and a flexible membrane can go a long way