Home Cuppa Convos Technical Snapshots Technical Snapshot: Challenges with Sheet Waterproofing Membranes
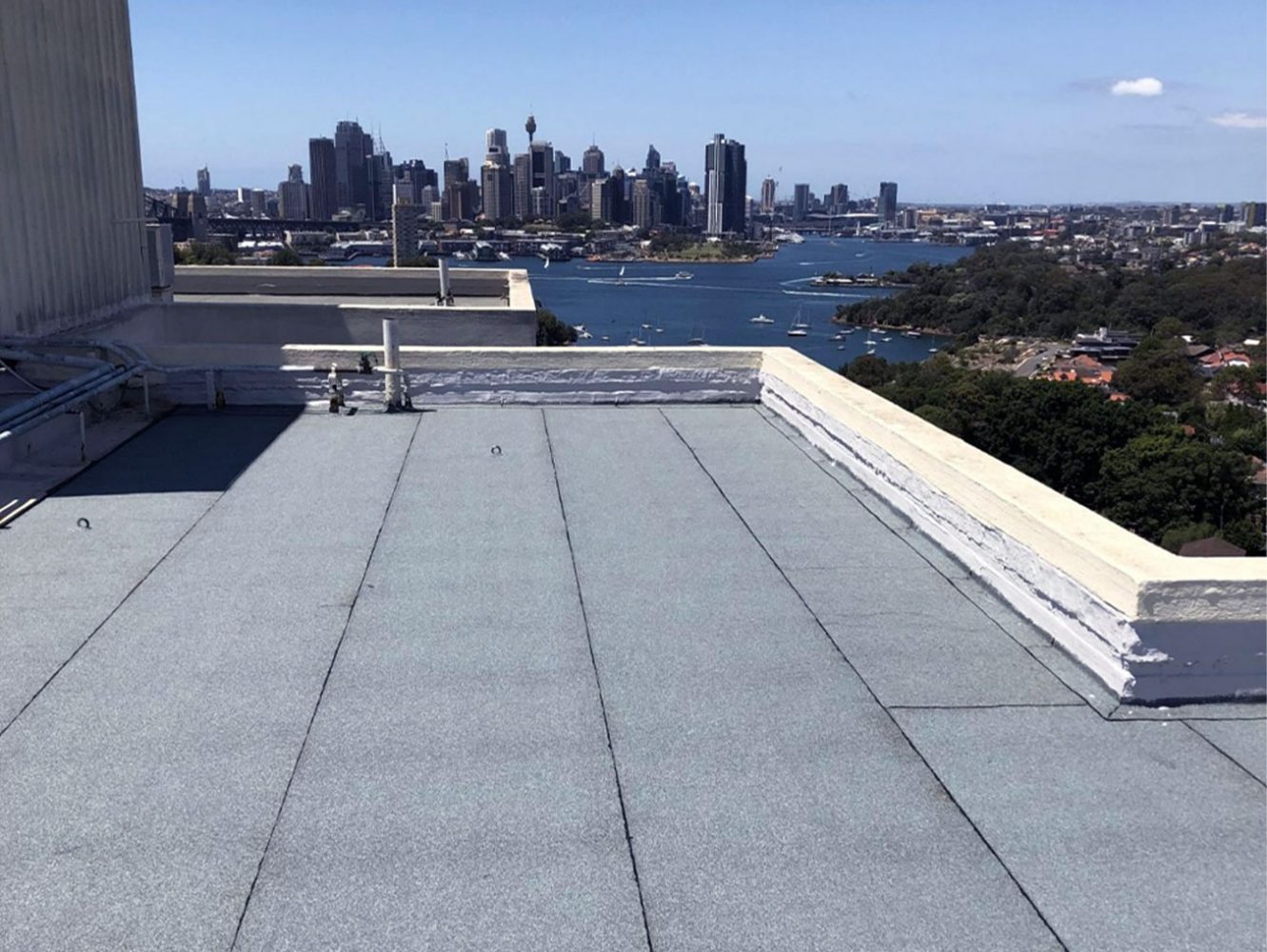
Technical Snapshot
Issue: Challenges with Sheet Waterproofing Membranes
Sheet membranes are a robust waterproofing solution, known for their consistent thickness and long life expectancy. Made from materials like Bitumen APP/SBS, PVC, TPO, Butynol, and EPDM, they are widely used in construction. However, improper handling or environmental exposure can lead to significant issues.
UV Exposure: When left exposed, non-UV stable membranes can crack and deteriorate, allowing water to penetrate and compromise the system. Proper UV protection, such as concrete toppings, ballast, or mineral finishes, is essential.
Installation Complexity: Installing sheet membranes requires a precise application. Common issues include:
- Insufficient heat and excessive cuts that penetrate through the base layer into the substrate below.
- Inadequately sealed seams between sheets, which increases vulnerability
to leaks. - Patchy installation with excessive torch application.
These problems increase the risk of water ingress and costly repairs, making it essential to ensure skilled labour, proper tools, and careful adherence to installation guidelines.
Material Selection: Different materials offer varying levels of flexibility, chemical resistance, and durability. Choosing the wrong material for specific conditions, such as high traffic or chemical exposure, can lead to premature wear.
Substrate Compatibility: Proper adhesion between the membrane and substrate is critical. Contaminated or uneven surfaces can cause delamination, diminishing the overall efficiency of the waterproofing system.
Incorrect
Pic 1. Insufficient heat and excessive cuts into the substrate layer
Pic 2. Seams between sheets not properly sealed
Pic 3. Patchy installation with excessive torch application
Solution
To ensure long-lasting and effective sheet membrane waterproofing, Bayset recommends following these key steps:
UV Protection: Cover non-UV stable membranes with concrete toppings, ballast, or mineral finishes to prevent cracking and deterioration from sun exposure.
Proper Installation Practices:
Ensure straight, uniform lines, correct overlaps, and staggered end laps during installation. Skilled labour is essential for achieving seamless application, reducing the risk of water ingress. Follow AS 4654.2 standards for junctions, lap joints, and seams.
Material Selection: Choose membrane materials that suit the project’s environment. For high-traffic or chemically exposed areas, consider durable options like TPO or EPDM for longer-lasting performance.
Substrate Preparation: Ensure the substrate is clean, even, and compatible with the membrane. Poor substrate conditions can cause delamination, so proper preparation is crucial for adhesion.
Ongoing Maintenance: Regular inspections and early repairs can prevent water infiltration and prolong the membrane’s lifespan.
AS 4654.2 states that ‘Laying membrane 2.6.1 Treatment of Junctions, lap joints, seams and cold joints shall be in according to the type of system and comply with minimum dimensions.’
Correct
Pic 4. Seamless installation ensures effective waterproofing
Pic 5. Continuous 10mm bitumen bleed at the side lap
Pic 6. Well-sealed seams prevent leaks